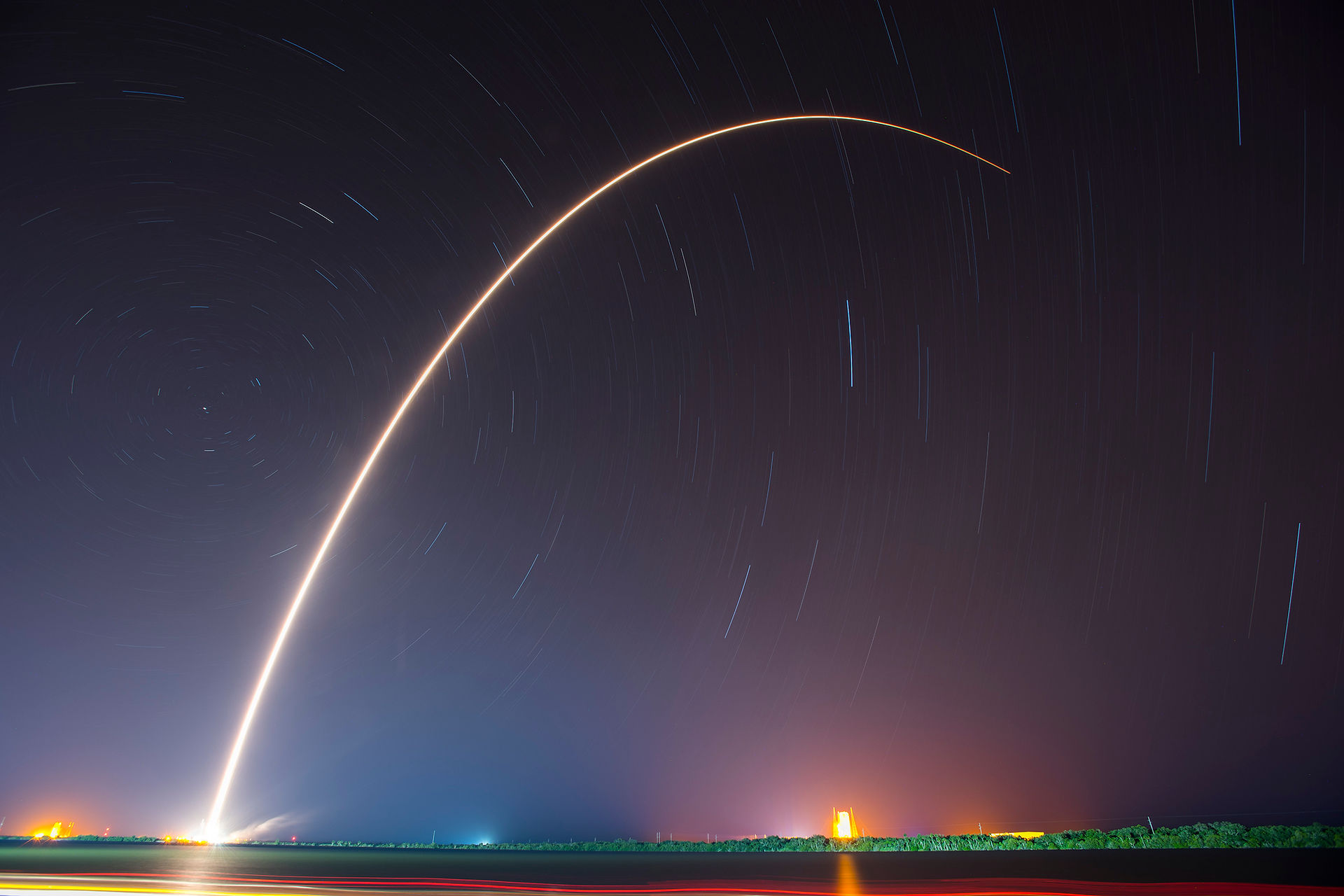
Aphelion Orbitals
Internship Projects
Aphelion Orbitals
Internship Projects
This page showcases the projects that I completed while I was an aerospace engineering intern at Aphelion Orbitals in Union City, NJ.



PROJECT 1: Filament Winder and Composite Pressure Vessel Test Articles
As an aerospace engineering intern at the launch vehicle startup Aphelion Orbitals, I worked extensively with the carbon composite manufacturing process of filament winding. I personally developed the company’s filament winding capabilities from no ability to the early stages of verifiable test articles. The process had several stages, all of which are documented below. Each step was completed based on goals set for me by the engineering team. I completed the work myself, with invaluable advice and support from the senior engineers.
-
Assembly: As the filament winder was delivered in individual components, save for the electric motors and motor controllers, I assembled the entirety of the machine over several days. Accompanying instructions and specifications provided large, discrete steps; consequently, I had to extrapolate many of the smaller assembly tasks from the general guide. Additionally, an upgrade module was purchased at the same time as the base model and the upgraded components had to be identified and incorporated into the build process.
-
Troubleshooting: After assembly and during startup and testing, several issues with the filament winder became noticeable. Each item was identified and addressed, usually through the process of modification, as described below. The process of modification was completed throughout the testing phases, as problems arose.
-
Modification:
-
The first modification completed was the addition of an extended bed. 16’ sections of extruded aluminum were inserted in the place of the stock 6’ beams. As a function of the increased bed length, the winder was now capable of producing 14’ long composite pieces.
​
-
Next, to move the machine from floor level to a workable height, uniform 3’ leg structures were assembled from scrap aluminum in the shop and affixed to the base of the winder bed.
​
-
Once wet (“wet” denoting the impregnation of the filament with an epoxy resin, as opposed to dry, no resin runs) winding tests began, it became clear that too much resin was being transferred to the filament, and consequently the composite part, during the resin bath. Too much resin produces a subpar part and is significantly more expensive – resin is a non-negligible cost. To address the problem, I produced custom wooden rollers, mounted on a machined, adjustable mechanism. This allowed for the rollers to be constantly readjusted, regulating the amount of resin supplied to the filament and overall part.
​
-
The winder delivery head consists of a channel and a guide roller, with two axes of control. At low winding angles (laying the filament in a direction closer to the lengthwise axis of the part, as opposed to high winding angle, which is laying the filament in a near-hoop pattern around the circumference of the part), the filament would slip from the guide roller and tear on the support structure. In response, I designed two vertical guide “bumpers” that kept the filament centered on the main guide roller and ensured proper filament placement on the part.
​
-
Later, it became clear that during 4-Axis Helical winds, with considerable rotation of the delivery head (~300 degrees of rotation, as opposed to previous 60 degrees rotations with the other winding regimes), the belt was slipping on the main delivery head gear. The gear provided was not matched to the belt, as the gear had been cut by the filament winder manufacturer and was not standard. Using a gear template for the belt, I created a gear that could be 3D printed in house. After several prototypes and adjustment for tolerances, a very inexpensive gear was produced that meshed perfectly with the belt and did not slip.
​
-
Dry Winding Tests: The trial parts that I designed and produced each served to test a specific function or process of the filament winder and carbon fiber composite. Every fiber composite part must be designed with the orientation of the fibers in mind. The direction of the fibers, or filament, will determine the material properties and strengths of the part. As such, each test article designed was composted of layers of filament, each laid at a specific angle. Through a combination of several varying-angled layers, a lightweight part could be produced that had strength in multiple dimensions. The angled pattern of each part was thus crucial to the success of the process. Initially, a basic layer was wound using dry filament – without any resin – to test the accuracy of the winding patterns on a subscale model.
-
Wet Hoop Tests: After the efficacy of the dry winding precision was confirmed, the simplest pattern had to be replicated with wet filament. These tests served to test placement while the fiber was wet, as the filament run through the delivery head differently while soaked in resin. The tests also involved the first use of the epoxy resin system, which consisted of a resin and hardener. When the resin and hardener were mixed, the resulting solution had a workable time limit, after which, the mixture would become unmalleable and unusable.
-
Wet 3- and 4-Axis Helical Tests: These tests built upon the Wet Hoop Tests but introduced increasingly complex winding patterns and more difficult low winding angles. The step up to 4-axis involved another motor and axis being integrated into the winding process.
-
Wet Full Scale Tests: Once the full range of winding patterns had been proved on a sub-scale level, the processes needed to be replicated on a flight hardware level. Several of the same patterns were completed on a full-size mandrel, with a 13 inch diameter.
-
Mandrel Removal: Integral to the winding process is the mandrel, which is defined as the mold in the shape of the final part upon which the filament in laid. The mandrel must either be removed after the winding process is completed or designed to be the first layer of the composite part. Due to cost concerns, it was decided that the mandrels used were to be removable. This proved to be difficult task, which was eventually solved by application of sealing and mold-release agents to the surface of the mandrel prior to winding.
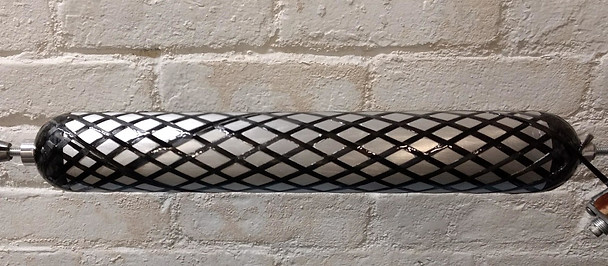

PROJECT 2: Assembly of Mobile Liquid Rocket Engine Test Stand
Worked with a senior engineer on the fabrication and assembly of a trailer-mounted liquid rocket engine test stand. During my time at Aphelion Orbitals, the company was working on creating a mobile stand to test their non-cryogenic, hypergolic, ablative engine. Built into the bed of a standard trailer, the test rig revolved around a thrust structure mounted near the rear. Plumbing trailed backwards from the injector on engine mount, through the thrust structure and valve systems, to the bases of the oxidizer and fuel tanks. Helium was used to purge the system. Electrical boxes containing the computer control system (Labview based) were attached on the front rail and supported by aluminum beams. A pressure readout panel was also located near the tanks at the rear of the system.
While I acquired basic familiarity with the entire system, there were several components on which I worked personally.
-
Tank Supports: Each tank was supported by an extruded 1.5in aluminum frame. The frames were designed to be individually stable in one planar axis and stable in the perpendicular planar axis when attached together. 3D printed inserts were placed into the rails of the horizontal crossbars to prevent movement of the tanks within the frames. Each frame was bolted to the bed using steel U-bolts.
-
Electrical Boxes: The Electrical boxes contained the custom computer system that controlled the actuation of the valve system, read pressures from the plumbing system, and read loads from load cells mounted beneath the tanks and behind the thrust plate on the engine mount. The electrical boxes were drilled out and mounted vertical beams
-
Fittings: I was charged with accounting for and cleaning the valve connections and plumbing components before assembly. Every component was cleaned, rinsed, dried, and sealed before use to ensure that no foreign particles were present within the plumbing system, which could react with the propellants. The plumbing system consisted almost entirely of AN fittings with a 37 degree flare or NPT fittings, used in conjunction with thread sealant. Solenoid values were used in both the oxidizer and fuel lines.
PROJECT 3: Small Solid Rocket Motor Test Stand
Designed a portable solid rocket motor test stand for testing new experimental solid propellant formulations as well as composite motor casings produced on the filament winder. The stand was designed to be both easy to manufacture and transport. Based on a frame of simple extruded aluminum bars, a load cell was to be affixed at the center of a large aluminum block, which was mounted on one end of the frame. Two clamping structures were placed along the frame, which served to lock the motor in place while firing. The clamping structures were designed to be easily produced in house on a CNC mill, out of quarter inch aluminum. Each structure incorporated adjustable arms that could accommodate motors with diameters of 2.5in to 6in. Wheels on the contact end of each arm served two purposes: 1) allowing for easy horizonal insertion and removal of rocket motors, 2) permitting the motor to slide within the clamping arms to account for the slight displacement of the load cell while firing. If necessary, the assembly could be anchored to the ground on site for more powerful tests.
Regrettably, I completed the internship period at the Aphelion before the test stand could be manufactured. As such, the design existed only in drawings and CAD files, all of which are proprietary and cannot be included in this portfolio.
Image Source: https://tinyurl.com/yyovfs8q