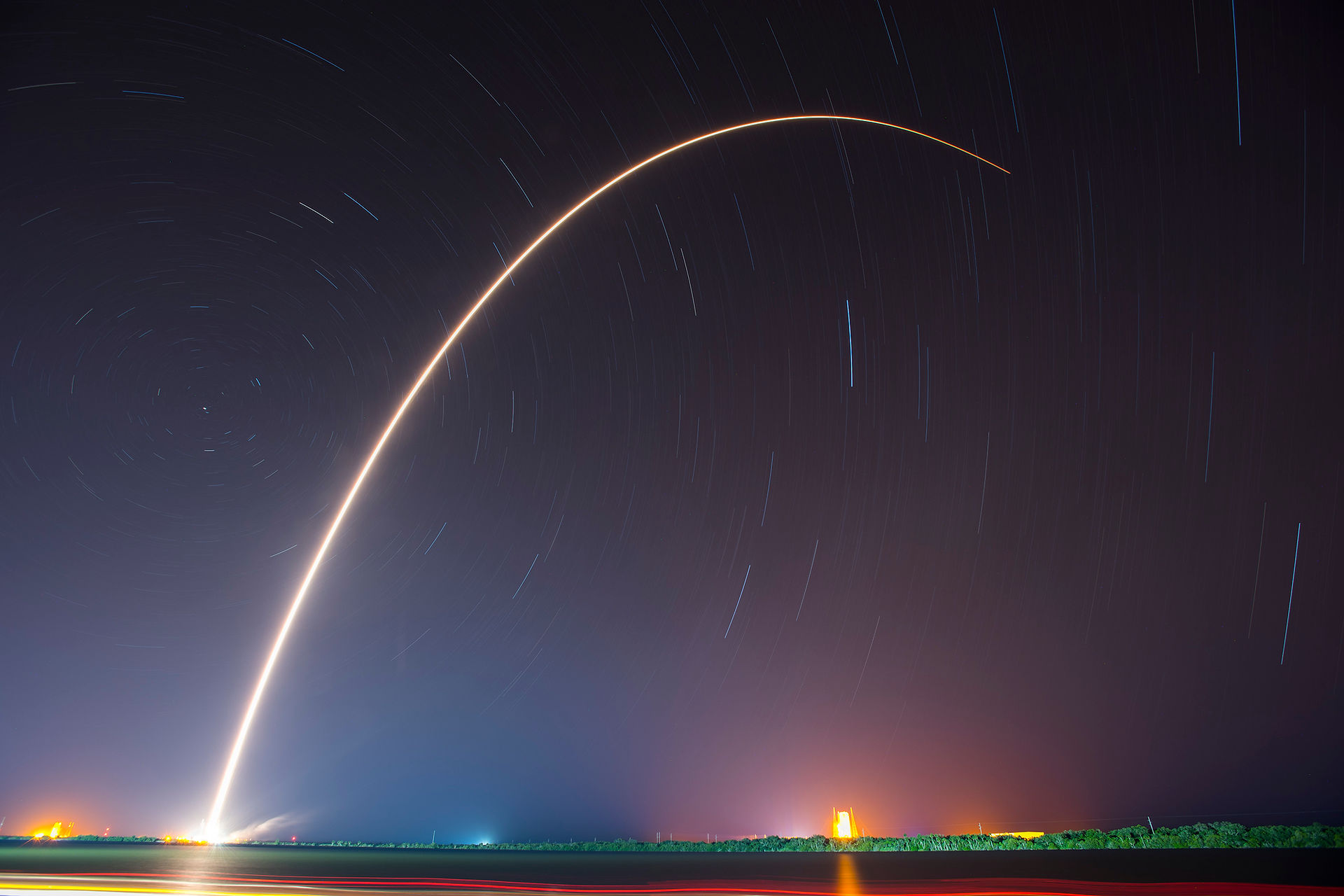
Tufts SEDS-Rocketry Projects
Tufts SEDS-Rocketry Projects
This page showcases the projects that I have completed to date while working on the Tufts SEDS rocketry team in Medford, MA.

PROJECT 1: Small Satellite Attitude Control System Prototype
For the Tufts Senior Design Course in the Fall of 2020, I proposed a project of my own creation which would serve as a proof of concept in satellite control systems while opening the door to fluid propulsion development at Tufts University.
​
I was responsible for designing the fluid system and nozzles, which would store, regulate, and dispense the compressed (3000 PSI) air for attitude (orientation) control maneuvers. The nozzles were utilized the converging-diverging layout, serving to accelerate the gas from subsonic to supersonic velocities and thus increasing the efficieny and performance of the entire system.
​
Development of the prototype system will continue in the Spring of 2021, with the stated goals of achieving closed loop control and vastly increased run time.
​
Finally, it must be acknowledged that the effort could and would not have been a success without the immense contributions of all team members, including Madeleine Oliver, Olivia Martin, and Harry Steinberg.
​
~
​
The full project report can be downloaded below.
​
​
​



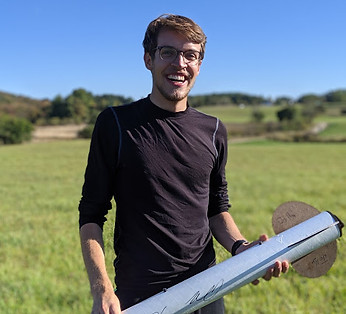
PROJECT 2: Space Bo I Rocket
As team lead and founder of the Tufts rocketry project team, I actively participated in and managed the development of the University’s first rocket, christened “Space Bo I.” Designed as a NAR Level 1 Certification Rocket, the vehicle was powered by a commercial I-class solid rocket motor. The rocket served not only as a qualification vehicle for team members to become licensed high powered rocket users, but as an introduction to basic aerospace engineering principles for the inexperienced members of the team.
Throughout the development process, I worked with groups of members organized into subteams, such as fins or propulsion structures, as well as individual members on smaller projects, like producing a detailed CAD model of the nose cone from the equation-driven geometry. Thus, I was involved in all levels of the project, from behind the scenes work like securing funding and working with faculty mentors, to collaborating one-on-one with project team members. I’ve detailed several such work sessions below.
-
Nose Cone: After performing research on nose cone geometry and considering our application, I decided on a Von Karman curve. With the goal set, I pulled in two junior members of the build team and walked them through the concept. Next, we modified the equation with our relevant measurements and moved on to CAD modeling. We found that the software we had been using did not easily support equation driven geometry. Consequently, we switched to a more advanced software and adjusted our equation to match the syntax and format of the program. This file was then further polished and sent to HP Labs for high quality additive manufacturing.
​
-
Avionics Bay: Controlling the deployment of the parachutes throughout flight is crucial to flight success. A commercial flight computer controls these the deployment events, mounted in the avionics bay. The avionics bay had several key technical requirements: secure mounting for the flight computer and power source, ease of removal, and pressure isolation from the parachute bay (to ensure that the pressure measured by the flight computer is not influenced by the deployment charges). After outlining these requirements, I brainstormed with build team members and produced concept drawings. Concepts were followed up with CAD models and Masonite prototypes.
-
Parachute Deployment Mechanism: Deployment events are controlled by the avionics bay, but the mechanism of release is separate. The main chute is very large and produces considerable friction with the body walls when being pulled from the rocket during deployment. Due to the friction generated, a prohibitive amount of force was needed to deploy the parachute. In response, I worked with my core team to design a specialized, constricting ejection bag for the parachute, which kept the cross-sectional profile of the packed parachute small enough to allow for easy deployment.
-
Motor-Fin Assembly: The rear internal structure of the rocket consists of a cylindrical frame that serves two essential functions: securing the motor and fins to the body as well as transferring the thrust of the motor to the airframe. I developed the requirements for the structure on my own and then handed them over to the subteam. I ensured that the team had the software tools and resources to complete the design. The fin geometry was iteratively created based on simulation in OpenRocket. I continued to work with the team regularly as they talked through the design, created each component in CAD and then combined the pieces, and finally produced Masonite prototypes in the machine shop.
Overall, the rocket performed well during flight. The parachute deployment mechanism of the vehicle had to be rebuilt on site due to complications, but the rocket flew and achieved a height of 2496 ft (safely under the altitude ceiling set by the launch site). The parachutes failed to deploy due to faulty placement of the ejection charge, however the flight was still considered a success as the ascent was flawless and the vehicle was recovered. In the future, a new avionics bay will be designed which will allow for optimum placement of the ejection charge to ensure proper chute ejection.
PROJECT 3: Jolly Wolly Wocket
In October 2019, I designed, built, and launched an NAR L1 high powered rocket in under 24 hours. This was a personal project, completed in part to test the performance of elliptical fins as well as the feasibility of rapid vehicle production. The hypothesis was that elliptical fins produce the least induced drag during passive restorative motion, when the fins are providing a restoring moment to the vehicle as the body is angled from the flight path. The elliptical shape produces most of the lift near to the body of the rocket, which decreases the wingtip vortex generated by the pressure differential above and below the wing (the lift), which is the cause of the induced drag.
​
A motor-fin assembly was designed in Solidworks and then exported as .DXF files for use on a laser cutter. 1/8" thick sheets of Masonite were then laser cut into the necessary components, consisting of the fins, struts, and centering rings. The overall design was verified using an OpenRocket simulation once the design was complete.
​
The vehicle experienced a flawless flight, with a straight ascent and chute separation just after apogee, at ~2100 ft. A slow descent followed by a gentle landing with no damage to any of the components made the launch a textbook certification flight.
​
Finally, It should be noted that the contributions to the assembly process by rocketry team member Jeffrey Blitt were invaluable.
​
