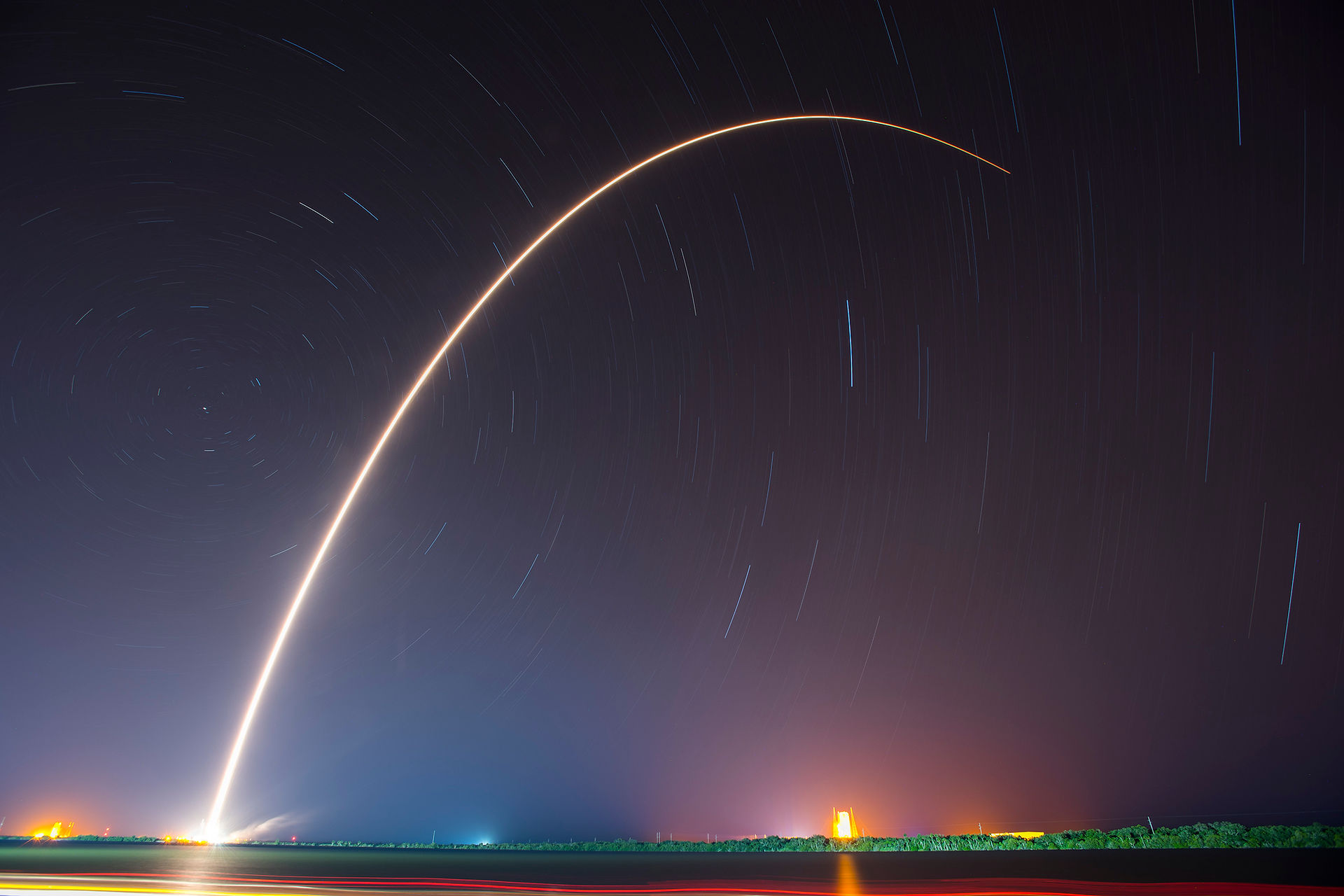
PPG Aerospace
Internship Projects
PPG Aerospace
Internship Projects
This page showcases the projects that I completed while I was a test engineering intern at PPG Aerospace in Los Angeles, CA.
PROJECT 1: Verification of New Production Process
Note: Unfortunately, many details of the projects completed while at PPG are proprietary. Thus, specific aspects of projects such as process descriptions, dimensions, and product/customers names are intentionally left out of this portfolio. These restrictions apply to projects 5 and 6 as well and are the reason that no pictures or diagrams are included.
Verified the material effects of a new production process that was introduced to the manufacturing operations of a jet canopy. The process was introduced within the CNC drilling and milling steps and the effects of the material of the canopy had to be studied to determine if the new process would produce products with similar or superior material properties.
Upon receiving sheets of the milled and drilled material from production, I worked with a senior engineer to determine the tests that should be completed. I then created a test matrix defining each test, along with the coupons (samples) of material that would be prepared for each test. I created and introduced a nomenclature to easily identify data from the tests and then began the testing campaign. While the tests were extensive and continued after the end of my internship, the initial results demonstrated that the new processes instituted produced parts with similar material properties as the prior process, thus verifying that the new processes could continue to be used without fear of increased damage to the parts.
PROJECT 2: Product Development Support Testing
Tested and completed technical report on the electrical characteristics of an in-development heating element. The customer wanted our development team to determine the effects of heating on current draw in the heating grid a certain windshield panel. Another intern and I were tasked with designing, executing, and reporting on an experiment to provide the customer with the data that they desired.
Two rounds of testing were completed, with the second round building on the first, bringing improved data recording, simplified test setup, and improved accuracy. We worked with senior engineers and management to fully define the test requirements and parameters prior to and throughout the testing process, refining every part of the test to optimize the validity and accuracy of the data. Thermal images and video cameras were used to thoroughly document the testing process.
A memo and a full technical report were produced and presented to management, detailing the test parameters, purpose, methodology, results, and analysis. The report followed complete company guidelines and formatting, derived from industry standards, and was met with approval. All of the requisite data was provided to the customer in a timely and transparent manner, with the experiment methodology satisfying their requirements soundly.
PROJECT 3: Quality Control Materials Testing
Worked alongside full-time members of the engineering test lab to complete quality control testing of parts from all stages of the product lifecycle, from early development to regular production. Tests were of the material nature and included tensile pull, crack propagation, lap shear, and peel methods. I cut and prepared coupons out of larger samples delivered from various stations throughout the production process. Results were meticulously documented and the reporting of out-of-spec parts fell squarely to members of the test lab, myself included.
Image Source: https://tinyurl.com/y3asjznx